Pandemic-driven shortages of semiconductors, which power everything from cell phones to gene sequencing to brake sensors, continue to disrupt every facet of the United States economy.
University of Miami Patti and Allan Herbert Business School experts, Sammi Yu Tang, associate professor of operations and supply chain management, and David Kelly, an economics professor and sustainability specialist, detailed the importance of the precious chips and assessed the current supply scenario.
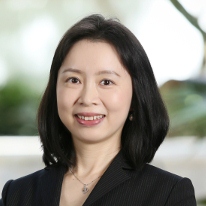
“The potential benefits of increasing the U.S. semiconductor manufacturing capability and capacity are enormous,” said Tang, noting that semiconductors are key components for technologies that power critical infrastructure such as energy grids, water systems, and communication networks—as well as military systems and technology-driven industries such as auto manufacturing, electronics, wireless networks, and medical equipment.
Building new manufacturing facilities and funding new research efforts will create new highly skilled jobs, she added, and increasing the viability of U.S.-based semiconductor manufacturing would obviously reduce the current heavy reliance on foreign suppliers for chip supply.
Currently, three quarters of production stems from four Asian locations—Taiwan, South Korea, mainland China, and Japan.
Tang explained that semiconductor production consists of several stages: design, manufacturing and assembly, testing, and packaging or ATP. She pointed out that the U.S. has been a leader in the design and development of new chips for years but has lost ground in terms of manufacturing.
In 2019, only 12 percent of the chips sold worldwide were made in the U.S. compared to 37 percent in 1990, according to a Wired report.
“The recent chip shortages that hit the auto industry and electronics industry have shown clearly how much the U.S. economy and the entire society are dependent on foreign suppliers,” Tang said. “This has triggered both the government and the industry to take action to try and increase the manufacturing capability and capacity in the U.S.”
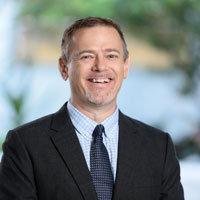
Kelly echoed the importance of the U.S. increasing its manufacturing capacity to safeguard security interests and key facets of the economy.
“From a national security perspective, chips are obviously important, both from weapons manufacturing and from the point of view of stealing designs and technological secrets,” Kelly said.
From an economic perspective, however, he pointed to a tradeoff between cost and resilience. Concentrating production lowers the cost per chip but makes the economy more subject to shocks like a plant going down, he noted, adding that it was difficult to determine the best balance between these ideas.
The only hurdles to relocation are scale and technological, and long-term the possibility exists that having too many plants worldwide would lower production and the potential for profit at each plant, according to Kelly.
“Production plants are extremely expensive and complicated to build, thus scale economies are huge,” he said. “You must sell a huge number of chips to pay off the fixed costs of building a plant. It follows that the solution is to build relatively few, but huge, manufacturing plants.”
Many chip designers and buyers can all use the same plant, further increasing scale relative to creating a plant to build the chips needed for one company, he added. Of course, fewer plants mean fewer locations, and less resilience if one plant goes down.
“Once the industry got started in Taiwan, the scale and complexity took off to such a degree that it became difficult to start competing facilities elsewhere,” he reported.
The more Taiwan produced, the more skilled they became, and the more difficult for competing manufactures to enter given their lack of expertise.”
He added that China has increased its production of late, essentially because the government has massively subsidized production. “This allows chip manufacturers to lose money due to small scale and still survive,” he explained.
Kelly referenced a Wall Street Journal article reporting that the U.S. government, attempting to level the playing field, has begun to copy the Chinese example and edge toward “industrial policy,” where government actions favoring certain industries shape the economy.
According to Kelly, the previous administration persuaded the Taiwan Semiconductor Manufacturing Company, the world’s largest foundry that makes the bulk of cutting-edge chips, to locate a new plant near Austin, Texas.
In early March, the Biden administration ordered a 100-day review of supply-chain vulnerabilities in four areas: semiconductors, batteries, pharmaceuticals, and strategic materials, the Wall Street Journal reported.
In June, the Senate passed the U.S. Innovation and Competition Act, which included $52 billion for the Creating Helpful Initiatives to Produce Semiconductors for America, or CHIPS Act. The initiative, which subsidizes the creation of new plants in the country, has stalled in the House.
Samsung last week announced that it was investing $17 billion to build a plant in Taylor, Texas, to produce high-end chips. The investment is the South Korean manufacturer’s largest in the U.S.
Ford Motor recently announced that it reached a partnership with GlobalFoundries, a U.S.-based chip supplier owned primarily by the Dubai government, to increase its short and long-term supply of semiconductors. GlobalFoundries has factories in Vermont and upstate New York.
Tang highlighted that the business model in the semiconductor industry has shifted to focus more on the design of chips with the manufacturing stage outsourced to these so-called foundries.
“As semiconductor manufacturing grows in cost and difficulty, massive capital investment is required to keep up with the advancement in chip designs,” she said.