Delegates at the high-stakes COP26 climate summit who are devising new strategies to lower global levels of greenhouse gases would be wise to address a major source of CO₂ emissions that made it possible for many of them to travel to the summit: planes.
In 2019 alone, CO₂ emissions from all commercial operations totaled 918 million metric tons, with 85 percent of those emissions coming from passenger transport, according to the International Council on Clean Transportation.
Now, a University of Miami researcher is helping to spearhead a project that could substantially reduce emissions of the man-made, heat-trapping gas from aircraft.
James Coakley, an assistant professor of mechanical and aerospace engineering in the College of Engineering, is attempting to create the next generation of high-temperature alloys—specifically, refractory metals that are incredibly resistant to heat and wear.
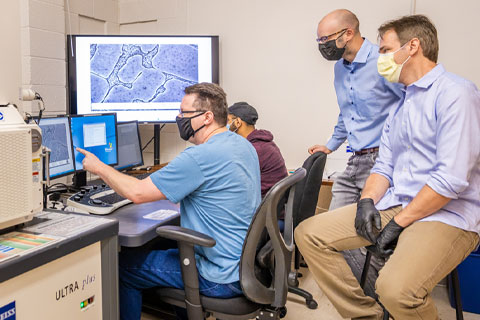
“Think of them as a new class of alloys,” said Coakley, who is collaborating with the U.S. Air Force and Cambridge University on the project.
“In aviation, the higher the temperature at which you can operate an airplane engine, the more efficient the engine will be,” he explained. “Less efficient aircraft engines burn more fuel, and burning more fuel translates to more CO₂ in the atmosphere. So, there’s a big push in the industry to increase engine efficiency, and that means going to higher temperatures.”
Excessive heat, however, can compromise the current generation of alloys used in engines, degrading their strength and durability to the point of failure.
Aerospace engineers have relied on nickel-based alloys for decades to make turbine blades, discs, and other critical aircraft engine components. “But we’re at the point where we’ve advanced those alloys as far as we can,” Coakley said.
And that’s where the new class of refractory metals he is helping to develop comes in. While refractory metals like tungsten and tantalum are well known for their resistance to heat and corrosion, they tend to be heavy, placing unneeded stress on aircraft engine components. “We’re trying to strike a balance between high-temperature properties and lightweight characteristics,” Coakley said.
So, combining different elements—for example, lightweight titanium with durable tungsten—to create a new type of refractory metal with multiple characteristics could be the key.
Coakley recently helped test such an experimental alloy at the legendary Oak Ridge National Laboratory in Tennessee. Combining mechanical loading with a furnace to simulate conditions inside a jet engine, he and a team of other researchers subjected the alloy to high temperatures and other stresses for different lengths of time. Simultaneously, they also monitored the new alloy with a neutron beam to determine if it would deform. Achieving higher tolerance to stresses and temperatures was the goal. Results are still being analyzed.
While Coakley is examining the special alloy’s bulk, his colleague, assistant professor Giacomo Po, is investigating the relationship between its macroscopic and microstructure properties. He is doing so by combining computational modeling with high-temperature micro- and nano-scale mechanical testing carried out inside a scanning electron microscope.
“This is an enormous challenge,” Po said. “We need to develop an alloy that is light, strong, and stable under unprecedented levels of stress and temperature. If the alloy fractures prematurely, then we need to figure out why. And micromechanical models and testing help us understand what features of the alloy microstructure result in premature failure,” he added.
“For the aviation industry’s efforts in reducing its carbon footprint, this project has huge implications,” said Oakley.